3D-tulostus mullistaa vaativien ortopedisten implanttien valmistuksen
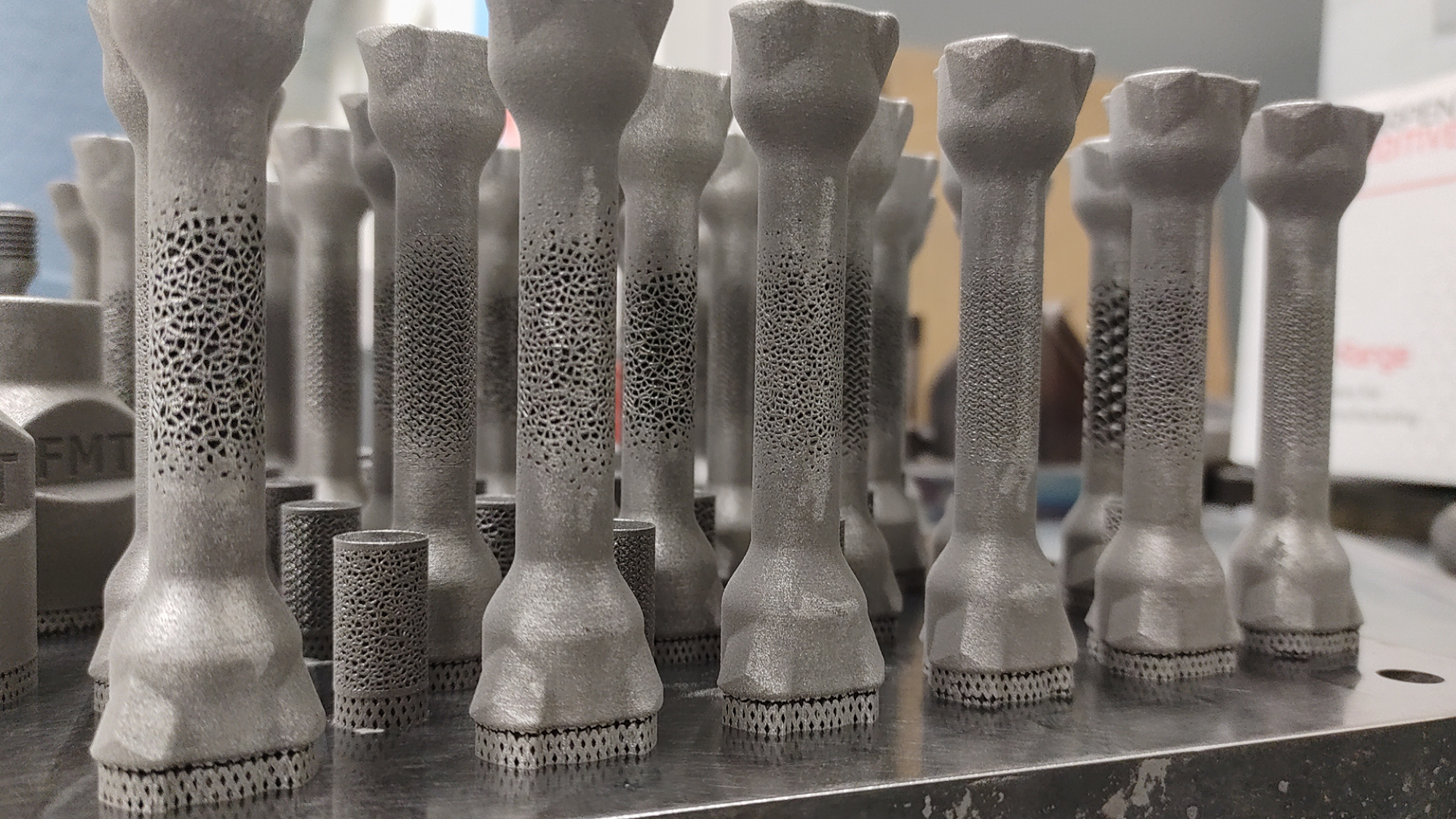
3D-tulostus yleistyy voimakkaasti metalliteollisuudessa. Lääketieteessä menetelmää on toistaiseksi käytetty jonkin verran muun muassa hammaslääketieteessä ja instrumenttien valmistuksessa. Uusia 3D-tulostuksen sovellusmahdollisuuksia tarjoaa vaativien ortopedisten implanttien valmistus, jossa tällä haavaa joudutaan käyttämään standardikokoisia koneistettuja implantteja ilman mahdollisuutta potilaskohtaiseen räätälöintiin. Oulun yliopiston Kerttu Saalasti Instituutti ja Costa Rican Institute of Technology kehittävät 3D-tulostusmenetelmää potilaan huomioiviin yksilöllisiin tarpeisiin.
3D-tulostus tarjoaa nopean prosessin mittatilausimplanttien valmistukseen. Menetelmän valmistustarkkuus ja lähes vapaa geometrian hallinta antavat täysin uudet lähtökohdat implanttirakenteiden kehittämiselle. Valmistusmenetelmän erityispiirteitä hyödyntämällä voidaan vastata perinteisten implanttien puutteisiin niin mekaanisten ominaisuuksien kuin biosoveltuvuudenkin osalta.
3D-tulostus mahdollistaa sellaisten monimutkaisten rakenteiden toteuttamisen, joita muilla valmistusmenetelmillä ei voi toteuttaa. Tällöin voidaan suunnitella esimerkiksi keveitä ja kestäviä rakenteita siten, että optimointi kohdistuu myös hyvin pieniin yksityiskohtiin.
”Ortopedisissä sovelluksissa teknisesti suurin haaste on metallien suuri jäykkyys suhteessa eri luutyyppien jäykkyyteen. Käytössä perinteinen kiinteä ja siksi jäykkä metalli-implantti rasittaa ympärillä olevaa joustavampaa luukudosta ja voi johtaa ennenaikaisiin vaurioihin”, sanoo Oulun yliopiston Kerttu Saalasti Instituutin tutkimusjohtaja Antti Järvenpää Tulevaisuuden tuotantoteknologioiden (FMT) tutkimusryhmästä.
Tulevaisuuden tuotantoteknologiat -ryhmä ja Costa Rican Institute of Technology ovat yhteistyönä tekemässään tutkimuksessa osoittaneet, että kiinteiden rakenteiden sijaan 3D-tulostamalla tarkoitukseen suunniteltuja huokosrakenteita metallirakenteiden joustavuus voidaan optimoida eri luutyyppejä vastaavaksi. Lisäksi huokoisuutta voidaan kontrolloida niin, että implantin pinnasta voidaan tehdä kestävyyden parantamiseksi osittain kiinteä, mutta kudosten tarttuvuutta ja rakenteellista joustavuutta varten huokoinen.
Kehitetty uudenlainen implantti hyödyntää molempia piirteitä niin, että se voidaan kiinnittää luuhun ahdistusliitoksena ilman ruuveja. Tällöin luukudos kasvaa implanttiin kiinni huokoisilta alueilta. Erittäin huokoinen implantin sisärakenne on erinomainen alusta esimerkiksi verisuonten ja hermokudosten kasvulle.
Menetelmällä voidaan merkittävästi lieventää kuormituksen aiheuttamia vahinkoja luun ja implantin rajapinnassa sekä pidentää implantin elinikää. Kehitettyä rakennetta voidaan hyödyntää yleisimmissä ortopedisissä sovelluksissa, kuten lonkassa, polvessa tai selkärangassa, mutta myös harvinaisemmissa kohteissa.
”Digitalisoitu prosessi CT-kuvantamisesta implantin valmistukseen mahdollistaa kirurgisen suunnittelun asiakaskohtaisesti. Asiakkaalle räätälöityjen implanttien kehittäminen mahdollistaa entistä paremman kytkennän ja säädön luun ja implantin välillä. Näin voidaan vähentää kirurgisen toimenpiteen aikaa, kustannuksia ja riskejä. Digitaalisena valmistusmenetelmänä 3D-tulostus on paitsi nopeuttanut implanttien valmistusprosessia myös parantanut tuotteiden laatua”, tutkija Miguel Araya Calvo Costa Rican teknologisesta instituutista kertoo.
3D-tulostusteollisuudessa tuotantoketju lyhenee, kun biosoveltuvuudelle usein välttämätöntä karheaa ja huokoista pintaa ei tarvitse enää tuottaa erikseen jälkikäteen tehtävillä pintakäsittelyillä. 3D-tulostus mahdollistaa pinnan räätälöinnin valmistuksen aikana.
Metallisten hilarakenteiden kestävyyskokeita on tehty Oulun yliopistossa laboratorio-olosuhteissa lääketieteen standardien mukaisesti lupaavin tuloksin. Esikliiniset kokeet on käynnistetty helmikuussa Costa Ricassa. Oulun yliopiston FMT-ryhmän tutkijat matkustivat sinne 3D-tulostettujen metallinäytteiden kanssa tutkimusvierailulle. Metallinäytteet asennetaan eläinten luihin mekaanista laboratoriotestausta sekä biosoveltuvuuskokeita varten.
Kerttu Saalasti Instituutin Tulevaisuuden tuotantoteknologiat -ryhmä (FMT)