EU funding of 2 M€ for a Nordic project for the development and implementation of metal direct energy deposition methods in companies - Universities of Oulu and Lappeenranta involved with a budget of 1.1 M€
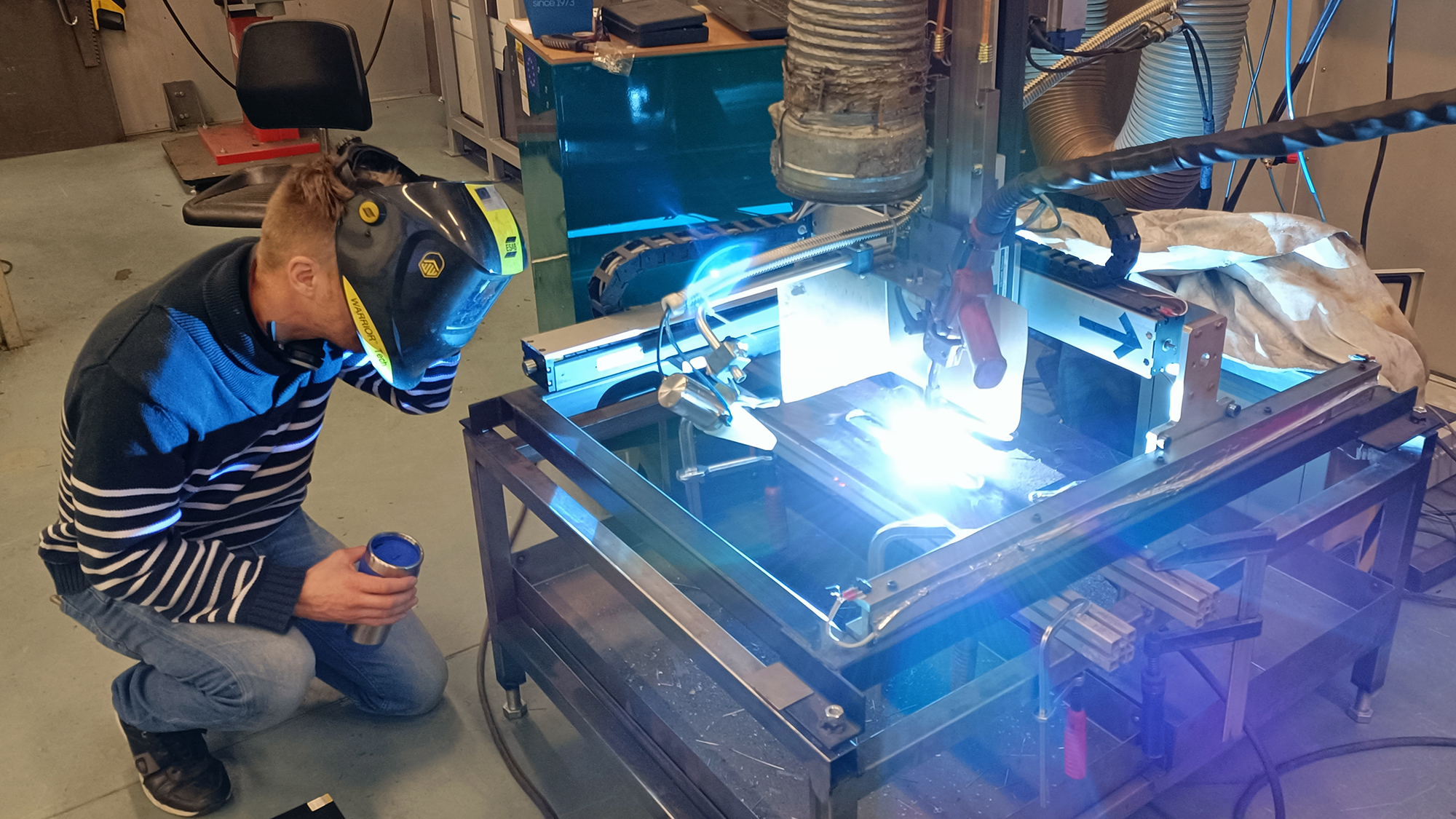
3D printing of metals by direct energy deposition is possible with modern robotic welding and CNC cells that are used in industry. The goal of the project is to promote the renewal of the engineering industry in the region by utilizing already existing equipment for the direct energy deposition of metals.
"Direct energy deposition methods have finally developed into industrially mature production methods. The starting point of the project is the industry's need to get more information about the possibilities and utilization of direct energy deposition methods. The project produces information on the management of the direct energy deposition process and the mechanical properties of the direct energy deposited structures. In addition to the best domestic expertise, we have very good international partners in the project and the support of international equipment manufacturers", says research director Antti Järvenpää from the FMT research group of the University of Oulu's Kerttu Saalasti Institute.
As a manufacturing technique, metal 3D printing is rapidly becoming more common, and its main techniques are the Powder Bed Fusion (PBF) and the Direct Energy Method (DED). Often, the acquisition costs of PBF equipment are still too high, but it is possible to use the direct energy deposition method with existing production equipment in industry. The direct energy deposition method is also a more usable method for manufacturing medium and large parts.
"For the sustainable development of the metal industry, it is important that the direct energy deposition becomes more common: it also accelerates the digital manufacturing revolution. The introduction of metal printing methods in companies is also one of the keys to maintaining security of supply during crisis situations, such as war or a pandemic, when global supply chains do not operate normally," says Järvenpää.
"The activities of the Future Production Technologies (FMT) research group of the University of Oulu's Kerttu Saalasti Institute, which started in 2004, focus on refining and transferring the good features of metallic materials into superiority of products using cost-effective manufacturing methods. 3D printing of metals is currently one of the group's main research areas. 3D printing research focuses on quality optimization. Here, fatigue resistance and the effect of print parameters and post-treatments on fatigue resistance is one of the most significant research areas," says Kari Mäntyjärvi, development manager of the FMT research group.
The modern research infrastructure of metal additive manufacturing/3D printing in Northern Ostrobothnia is mainly done in ELME Studio in Nivala and is supported by the up-to-date research laboratory of steel research center CASR on the University of Oulu's Linnanmaa campus.
"Research cooperation is carried out in the network in close cooperation with companies. Nordic research partners are involved in the consortium of the IDiD project, and the operation is supported by a significant number of international partner companies," says Mäntyjärvi.
The IDiD project will be implemented between January 1, 2023 and December 31, 2025. In addition to the Interreg Aurora funding program, the project is being funded by the Federation of Lapland, the city of Nivala, Nivalan Teollisuuskylä Ltd and two Finnish companies.
More information:
Kerttu Saalasti Institute, University of Oulu, FMT Research group
Antti Järvenpää, research director
antti.jarvenpaa@oulu.fi, +358 40 6720544
Kari Mäntyjärvi, development manager
kari.mantyjarvi@oulu.fi, +358 400 843050
Mikko Hietala, project manager
mikko.hietala@oulu.fi, +358 40 7547135