University of Oulu develops new types of orthopaedic implants using metal 3D printing
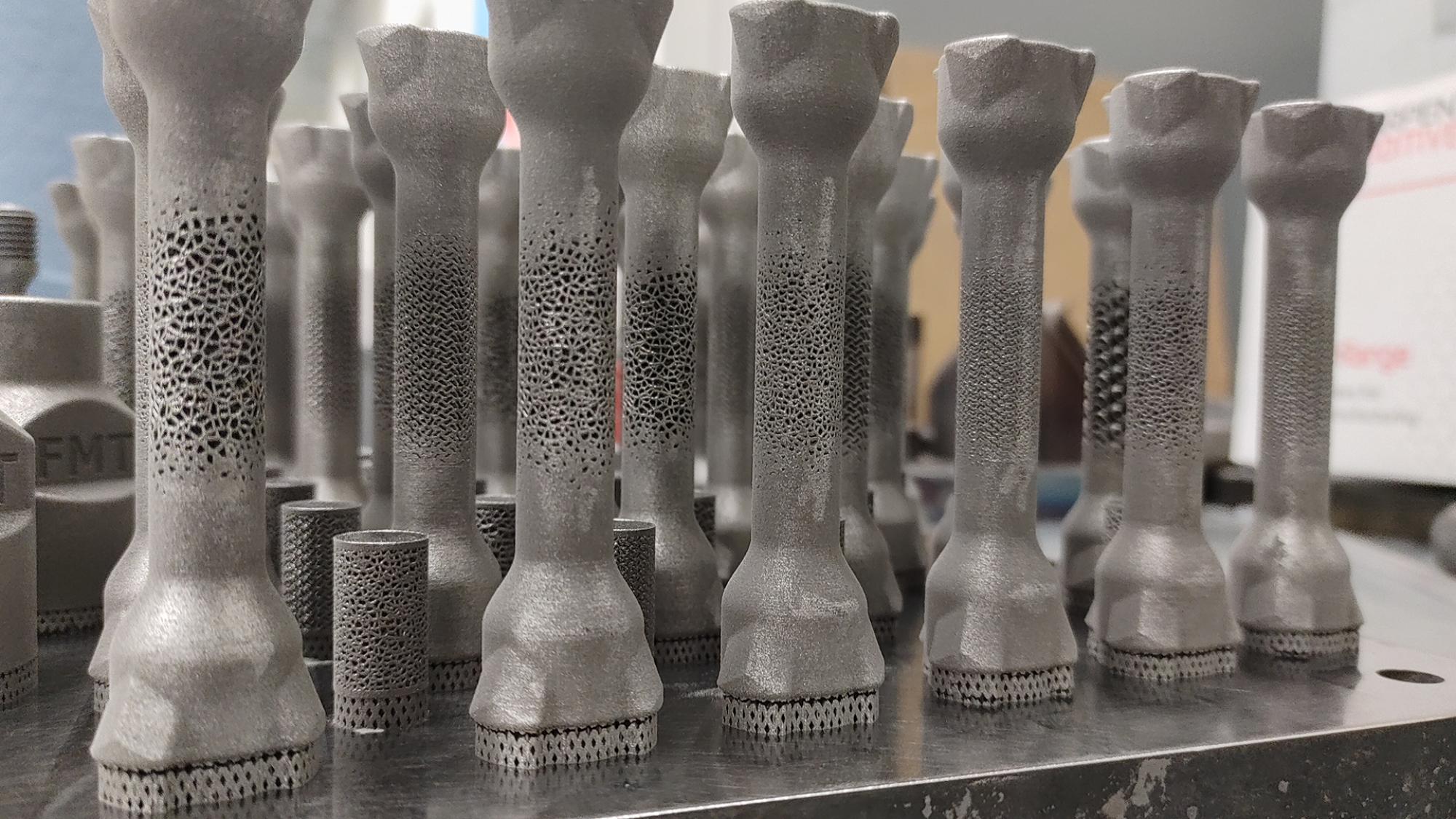
Personalised pore structures enabled by 3D printing allow the mechanical properties of implants to be optimised to resemble bone. In this case, biomechanical stimulation enables bone tissue growth in the implant, promoting osseointegration, mitigating stress damage at the bone-implant interface and extending the life of the implant.
"The development of custom-made implants allows for better coupling and adjustment between bone and implant using osseointegration. Furthermore, the digitalised process from CT imaging to the fabrication of a customised implant will enable the implementation of custom interventions such as surgical planning and the development of customised guides that reduce the time, cost and risk of the surgical procedure," says researcher Miguel Araya Calvo from the Costa Rican Institute of Technology.
As a digital fabrication technique, 3D printing has been integrated with existing CT scanning systems to allow imaging to be used to create digital models. This has led, above all, to a faster manufacturing process, but also to improved product quality.
"3D printing enables the realisation of complex structures that cannot be achieved by other manufacturing methods. This allows, for example, the design of lightweight and durable structures, with optimisation focused on very small details. So you go from the macro to the micro level. This can be used in different application areas, such as medicine," says Kari Mäntyjärvi, Development Manager of the Future Manufacturing Technologies (FMT) research group at the Kerttu Saalasti Institute, University of Oulu.
In the 3D printing industry, research groups' perspectives on the advantages of the digital manufacturing method are shared. Anna Sailor, Additive Manufacturing Consultant at EOS, also points out the productivity benefits made possible by reducing the production chain. "The production chain is shortened when the rough and porous surface - which is often necessary for biocompatibility - no longer needs to be produced separately with subsequent surface treatments, as 3D printing enables surface customization during manufacturing."
Deficiencies in traditional implants can be corrected with 3D technology
3D printing offers a fast process for the manufacture of bespoke implants, using a similar process that has already been commercialised by dentistry. 3D printing's manufacturing accuracy and near-free geometry control provide a completely new starting point for the development of implant structures. By exploiting the specificities of the manufacturing process, the shortcomings of traditional implants, both in terms of mechanical properties and biocompatibility, can be addressed. In orthopaedic applications, the main technical challenge is the high stiffness of metals in relation to the stiffness of different bone types. In use, a traditional fixed and therefore rigid metal implant puts stress on the surrounding more flexible bone tissue, leading to premature damage.
Research by the Future Manufacturing Technologies (FMT) group at the University of Oulu in collaboration with the Costa Rican Institute of Technology has shown that by 3D printing purpose-designed pore structures instead of solid structures, the flexibility of metal structures can be optimised to suit different bone types. In addition, porosity can be controlled in a gradual way so that the implant surface can be made partially solid for durability but porous for tissue adhesion and structural flexibility.
The new type of implant developed takes advantage of both features so that it can be fixed to the bone as a constrained connection without screws, as the bone tissue grows into the implant from the porous areas. The highly porous inner structure of the implant, in turn, provides an excellent platform for the growth of different cells such as blood vessels and nerve tissue. In addition, biocompatibility can be effectively influenced by optimising the shape and size of the pores, a feature that only 3D printing offers at this scale.
Trials in Costa Rica and Oulu
Durability tests of metallic lattice structures have been carried out at the University of Oulu on a laboratory scale according to medical standards with promising results. Pre-clinical trials will start in February in Costa Rica, when researchers from the University of Oulu's FMT team will travel with 3D-printed metal samples for a two-week research visit. The metal samples will be mounted on animal bones for mechanical laboratory testing and biocompatibility experiments. Further development of the fluidic structures and research into new alternative materials will continue at the University of Oulu, but it is hoped that the collaboration will also lead to clinical trials in Finland and Costa Rica in the coming years. The developed structure can be used in the most common orthopaedic applications such as hip, knee or spine, but also in less common sites.
"Active research collaboration and good personal relationships have contributed to the rapid development work. Cooperation has been smooth not only with Costa Rican researchers, but also with domestic industry, such as EOS Finland Oy, which is developing a 3D printing process, and the FAME ecosystem, which is developing industrial cooperation," says Antti Järvenpää, Research Director of the Future Manufacturing Technologies (FMT) research group at the Kerttu Saalasti Institute of the University of Oulu.
The FAME Ecosystem aims to speed up the utilization of 3D printing in Finnish industry by bringing together all experts in the field to share information with each other, to unify the field of research in the field and to strengthen cooperation between industry and research institutes.
"Research institutes and research groups play an important role in cooperation, because high-quality research is key to developing technology and finding more application sites. FMT does a really valuable job here by bringing the latest research results to the attention of companies, for example through various information sharing events," says ecosystem director Eetu Holstein from DIMECC Ltd.
Intelligent design tool under development
Alongside the practical research work, the research collaboration includes the development of an intelligent design tool. The tool under development will combine the loading conditions and mechanical requirements of different orthopaedic implants with the geometry data of the CT image to create a customised implant for the customer using the lamellar structures. The aim is to speed up the implant design process and optimise the usability of the implant.
The Kerttu Saalasti Institute at the University of Oulu's Nivala campus is planning to establish an RDI environment for the further development of new types of brick structures. The aim is to bring together experts from the fields of production and materials engineering and medicine to further develop new orthopaedic applications and to start clinical testing in the area.
"Various lattice structures are currently commonly used in the development of medical implants. The medical industry, which uses 3D printing, classifies the manufacturing of lattice structures as revolutionizing the industry", describes Anna Sailor.
More information:
Antti Järvenpää
Research Director
University of Oulu, Kerttu Saalasti Institute, Future Manufacturing Technologies research group (FMT)
antti.jarvenpaa@oulu.fi
+358 44 555 1633
Kari Mäntyjärvi,
Development Manager
University of Oulu, Kerttu Saalasti Institute, Future Manufacturing Technologies research group (FMT)
kari.mantyjarvi@oulu.fi
+358 40 084 3050